top of page
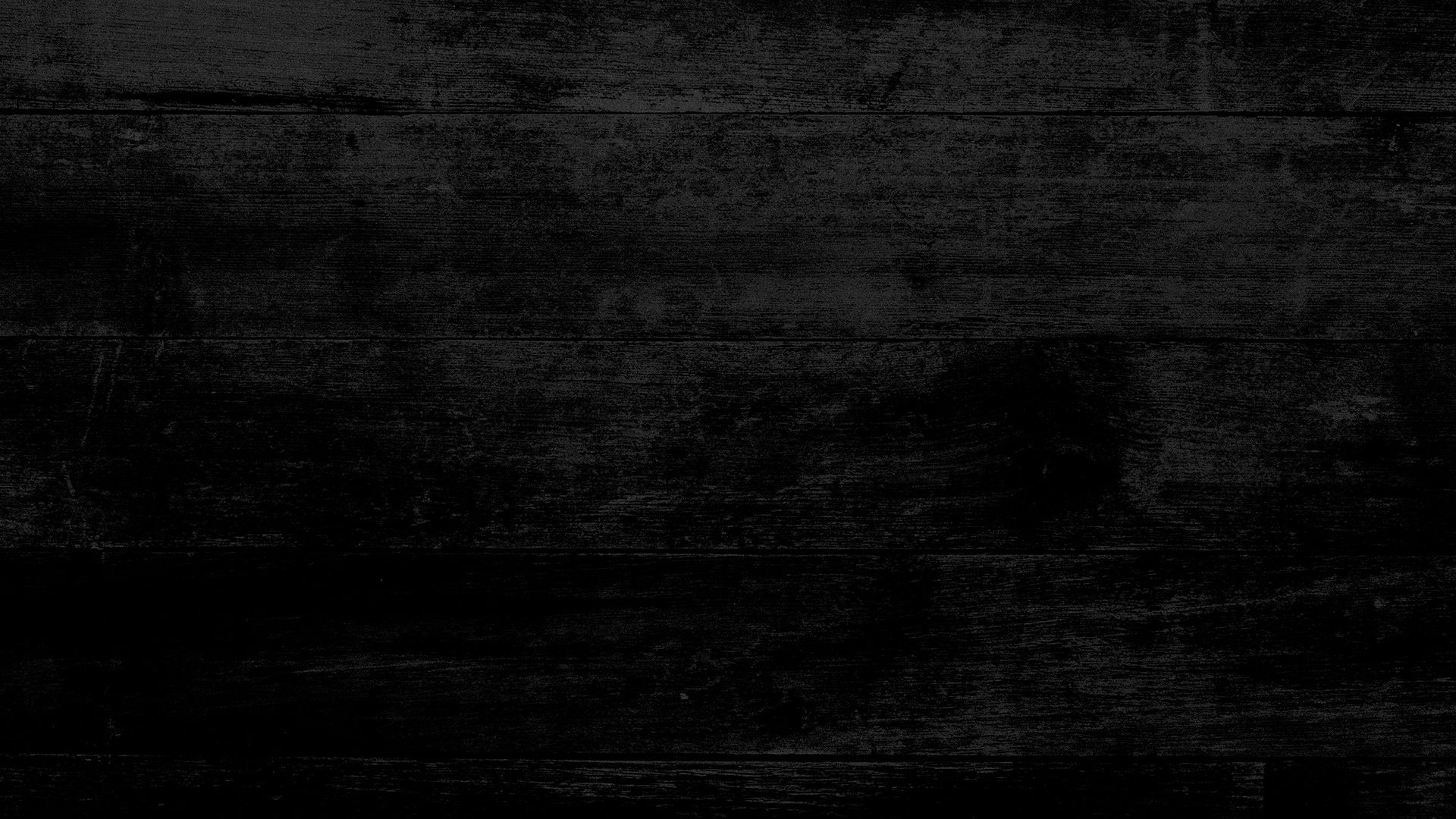
zoll medical corporation
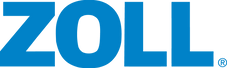
rfid
RFID Implementation Plan
Purpose: Real-time tracking of assets and production units to reduce time spent in locating them
Scope:
-
Removing route tags from units
-
Removing MIRS sheets and Move Tickets​
-
Automating transactions from MES to Oracle
-
Enabling quick and accurate location tracking of units and assets
-
Enabling customers and service depots to track units after sale
​
Plan:




RFID Configuration
Solutions provider conducts site surveys to their satisfaction, installing hardware to test out the POC is recommended. This helps to gain understanding of how the devices and software will communicate, as well as understand the database design requirements.
Fixed readers act as computer hubs to translate the signals from the antennas into aggregated data. This data includes location updates by zone (configured antenna ID), asset status (configured by workflow based on location), and time-stamp for last update (configured by mobile reader user credentials or antenna ID).
Cost and ROI Calculations:
Quotes for the equipment, hardware installation, site survey, and software development pricing were gathered from the solutions providers. These were analyzed and requirements were modified to get the most optimal cost.
Parallelly, internal cost savings were calculated through time studies of how long engineers spent locating NCR units and supervisors spent for purge searches, as well as operators who spent printing and attaching MIRS sheets to FG units at Sequence 130 before sending them to shipping, where their barcodes were again scanned to manually input into Oracle.
All these processes were not individually time-consuming but the volume of production increased the total time spent significantly. Long-term ROI would be promising.
robar
Product Labels Standardization
Purpose: Standardization of label creation process and prevent operators from having to create labels on the line when needed, reducing frequency of errors.
Scope:
​
-
Create product labels in BarTender
-
Program barcodes to pull product data directly from Oracle Agile
-
Store new label in Robar so operators can print through MES on the line without manual changes
​
Process Steps:

Torque driver
Torque Driver Initialization on New Product Line
Purpose: Torque drivers needed to be calibrated and properly installed on new product assembly line. The torque driver assembly configuration also needed to be replicated on other product lines.
Scope:
​
-
Update batch programs for correct torque parameters for each assembly sequence
-
Generate BOM and COGs for torque driver assembly configuration
-
Generate BOM of fabricated installation fixtures for future builds on other product lines
​
Torque Driver Assembly Configuration:

assembly tool
Wire Saddle Insertion Assembly Tool
Purpose: Operators were having trouble inserting a small wire saddle into a hole on the Main System board of one of the AEDs. This assembly tool would help operators insert the wire saddle without hurting themselves.
Scope:
​
-
Create FRD (Fixture Requirement Document) to understand the need and constraints for the tool
-
Design and 3D print prototype to test operation
-
Improve design and finalize with a FD (fab drawing), which is released with a Validation Plan
-
Create an engineering memo to qualify the tool for release to production use
​
​
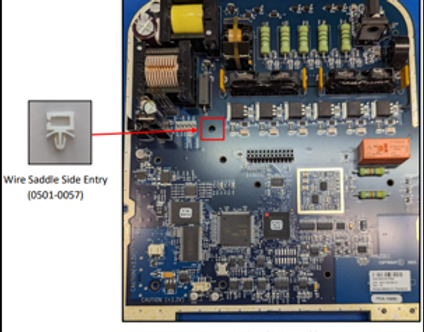
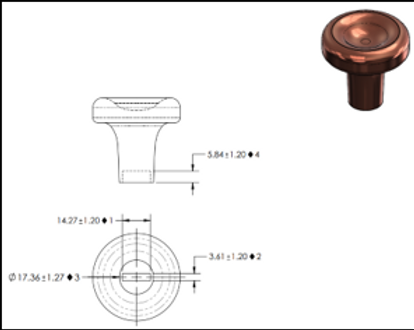
Image from FRD
Fab Drawing

Operational Use

Clearance from PCB Components
The Validation Strategy states that the tool must meet the Fab Drawing requirements and all nominal dimensions must be measured with a calibrated measurement tool. Minor changes to plan or protocol deviations can be described, assessed for their root cause, and provided with corrective action in a Validation Report.
There are no necessary OQ due to no critical functions in the process, only IQ and PQ. To perform the PQ, a functional memo for design verification will be written as a Validation Report to release the fixture to production. The design verification results must meet the acceptance criteria mentioned in the FRD. To perform the IQ, the Validation Strategy needs to be followed.
Cosmetic Damage Report
heat map

Regular data collection of cosmetic damages causing NCRs for the AED 3 units were performed for 3 shifts. This data was aggregated in an Excel spreadsheet with the areas referenced in the heat map, and a PivotTable and Chart is created to highlight the areas of concern.
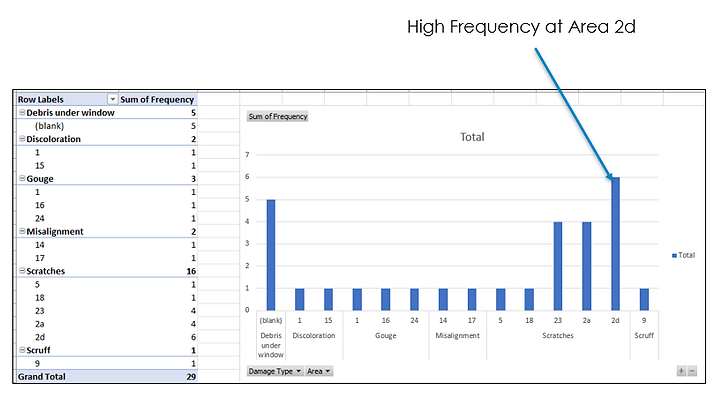
This data can be used to conduct root-cause analysis and resolve issues that were creating NCRs on the line, improving yield.
bottom of page